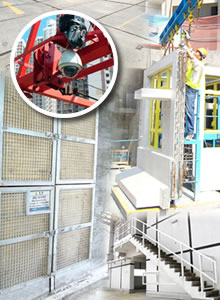
We actively incorporate contract initiatives to foster good work practices and thereby help improve working conditions on site. Many of these initiatives went beyond basic legislative requirements at the time they were launched.
Mechanisation and prefabrication
|
---|
The widespread use of mechanisation and prefabricated building elements in our construction projects has helped significantly reduce the risks to workers working at heights. This coupled with reduced reliance on timber in the industry has also improved efficiency and quality control, while reducing construction waste and pollution on site. Hard paving areas in construction sites
To enhance handling and storage of materials or components in a safe and orderly manner, we specify the use of hard, levelled and well-drained paving in numerous areas on site. These include: the main haul road, exit points with vehicle washing areas, and material handling and storage areas. The hard paving material, including concrete hard-paved material, precast concrete slabs and steel decking, may all be used in the construction of these hard paving areas. Adoption of hard paving also brings improved accessibility, minimizes ground damage, reduces contamination and provides a safer haul road for vehicular traffic and better separation of pedestrians and vehicles. Moreover, the overall physical conditions on site and in the immediate environment are improved in terms of cleanliness, dust control and hygiene. Full-height steel gates in lift shaft openings
We mandate temporary full-height steel gates, in all lift shaft openings in new works contracts to help prevent persons and/or objects falling into the lift shaft. To allow egress of persons working inside the lift shaft, these gates shall be closed at all times and could be locked from outside but should be readily opened from the inside the lift shafts at anytime, without the need of a key. Additionally, the temporary steel gates shall consist of 4-leaf doors with an upper pair and a lower pair of doors. Physical means to enhance safety in lifting management
To reinforce safe lifting operations, numerous enhancement measures have been introduced. These include specifying: the use of video surveillance and audio alarm systems in lifting zones, the use of logbooks, adoption of computerised systems for round-the-clock surveillance, and the issue of ‘permits to work’ for on-site staff and related personnel carrying out special lifting operations. Non-smoking policy
We mandate that a non-smoking policy be stipulated in the safety plans of all our contractors, including rules on the prohibition of smoking on site. For sites without a full prohibition of smoking, designated smoking areas—with associated provision of fire fighting appliances and cleaning services—need to be clearly stated in the policy. Staircases to main and upper roof areas
Slanting staircases as well as working platforms are provided for safe access to main and upper roof level for operation and maintenance of the services. This avoid high catladders and enhance safety to the frontline workers. |